Japanese Datsun fanatic PAMS Japan (http://pams-japan.com/30cafe/project.php) has created a new high performance cylinder head for Datsun L6 engines. The head has been manufactured by JMC (https://www.jmc-rp.co.jp/en) utilizing very high quality standards. You can find more detailed information about the cylinder head below. We are proud to work with them. Please contact us when you like to get yours.
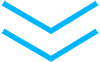
An L-type 6-cylinder engine that has been loved both in Japan and overseas for about 50 years. In its long history to this day, there are many wonderful tuning menus that can be said to be the crystals of wisdom left by our predecessors.
The old-fashioned normal L6 with turn flow & 2 valves is a powerless engine that is not suitable for sports cars, but once a tuning scalpel is inserted, it transforms into a different engine that hits 100 to 120 PS or more per liter. It has potential. However, some hurdles had to be overcome in order to carry out the ultimate L-shaped mecha tune.
Among them, the most problematic ones are the part of shaping after applying argon welding to the combustion chamber and the port polishing with the capacity expanded to the limit. They have risks such as thermal distortion of the head body due to argon welding to the combustion chamber, penetration trouble to the water jacket at the time of port polishing expansion processing, and there are few tuners that can complete the processing, and it takes years to complete.
There was also the problem that it took a long time in. In addition, the number of N42 heads in excellent condition has decreased year by year, making them valuable, and it has become difficult to secure a base head, which is one of the reasons for raising the hurdle to tuning.
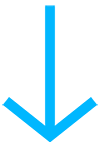
If so, we would like to optimize the water jacket for cooling by providing a sufficient port wall margin while realizing the ideal port diameter and shape with the ideal combustion chamber shape and volume from the beginning. If such a head could be newly designed and manufactured from scratch, wouldn’t it be free from the above-mentioned depression?
The delusion that could be called such a dream story was nothing more than a rice cake drawn in a picture before the gathering of L head project members. Here, I would like to briefly introduce the basics from the start of the project to the completion of the head, and I hope that everyone will warmly watch over this magnificent delusion.
WHY DO YOU NEED
JMC L6 HEAD ?
To find the ideal combustion chamber shape and volume while setting the head height to 108 mm, which is the same as the genuine one, the thickness of the upper surface of the head has been increased by 1.2mm while 1.2 mm has been removed off combustion chamber bringing valve closer to the piston side. It has been designed with the common troubles in mind caused by surface grinding, such as ones related to cam chains that often occur due to the usage conditions of various commercially available camshafts.
After analyzing the material of the normal head, we adopted AC4CH for higher strength and durability, and then applied T6 heat treatment.
While forming a big port, the margin thickness to the water jacket is set to 3.5 mm for IN and 3.0 mm for EX (* approximately 2.15 mm only under the IN spring seat), to improve safety against troubles (port wall holes/cracks into water jacket).
The combustion chamber is formed by the latest 5-axis CNC machining, and the shape and combustion chamber volume between the cylinders are the same.
The port core used to form the port during sand casting has been created by 3D printer to achieve a precise and consistent casting surface and high dimensional accuracy.
The diameter of EX port 3&4 has been adjusted to the same size as other cylinders with the aim of making the exhaust flow velocity consistent.
The design of the protrusion, that is caused by the escape part of the head bolt, inside of the port has been changed to a smooth shape during the sand-casting process, and that improves the flow rate.
Engine hanger mounting bolt hole has been created on the manifold side.
Direct ignition coil mount base bolt hole has been created.
A compact combustion chamber is achieved while keeping the standard head height at 108 mm same as the normal N42, which makes it possible to build an engine with a high compression ratio specification without the surface grinding being performed. In addition, the risk of gasket troubles caused by the decrease in head surface thickness is significantly reduced.
By eliminating the unevenness on the top surface of the head as much as possible, the shape is designed so that unnecessary oil pools are unlikely to occur.
After analyzing the water jacket of the genuine head by the detailed CT scanning being performed, a newly designed water jacket takes into consideration efficient and even cooling. The jacket capacity has also been increased by approximately 1.5l, and water channels have been provided in areas where they have not originally existed, enabling even and consistent cooling between cylinders.
Technical Specifications (ver. JP)
Cylinderhead casting | New casting |
Material | AC4CH |
Casting method | Sand Mold low pressure casting |
Heat reatment | T6 |
Port size | Intake: 41->38->43,5mm seat ring inner diameter |
Exhaust: 40mm vertical, 31,5mm horizontal | |
Port wall margin thickness | Intake 3,5mm / Exhaust 3mm (against water jacket), Intake valve spring under the seat surface 2,7mm. Head bolt part 1,8mm. |
Head bottom surface margin thickness | 11mm (against water jacket), Exhaust: except the small segment of the lower part 6,8mm |
Reference head height | 108mm |
Combustion chamber | 5-axis CNC machined (heart shaped), 38cc +-0,1cc |
Water jacket | New water jacket design based on full CT scanning internal analysis to optimize the cooling efficiency |
Valve seat ring material | Type A: NA. Type B: Intake/Exhaust special heat resistant steel. Type C: Beryllium Copper |
Seat ring hole diameter/depth | Intake: 47,5mm (-0,05-0,07mm) Exhaust: 39,2mm (-0,05-0,07mm) / Depth: 8mm (+-0,05mm) |
Valve guide material | Type A: NA, Type B and C: intake aluminium bronze, exhaust phosphor bronze |
Valve guide hole diameter | Intake/Exhaust 12mm (+0,01mm) |
Adaptive valve diameter | Type B/C: intake 46mm, exhaust 38mm |
Adaptive valve diameter | intake 46mm / exhaust 38mm |
Pricing
Ver. JP, Type A 4850eur
All combustion chamber processing work has been completed by 5 axis CNC machining, and this is the most suitable type for making a head that implements each tuner’s know-how, such as selecting a valve guide / seat ring according to the purpose, changing the port shape, or polishing the port wall. The valve guide holes, seat ring grooves etc. have been machined, but the valve guides and seat rings are not included.
All prices are vat 0% prices and subject to change depending on currency variations.

Ver. JP, Type B 5500eur
In addition to Type A, valve guide press-fitting of IN / EX seat rings, and seat cutting after press-fitting have been performed. Special heat-resistant steel is used for the seat ring, and the specifications emphasize durability.

Ver. JP, Type C 5800eur
In addition to Type A, valve guide press-fitting of IN / EX seat rings, and seat cutting after press-fitting have been performed. Beryllium copper alloy is used for the seat rings, and the specifications ensure higher performance while considering durability.
How to order
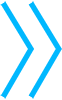
Please contact us to determine the most suitable shipping option or local pick up for you. Once that is clear we will send you a pro-forma invoice. Shipping with a tracking number happens after the payment. Please note there is no warranty or return right due to the nature of the products.
CONTACT: info@team23racing.fi
Questions & Answers
Q: What about intake or exhaust manifolds? Are they included?
A: No. JMC L6 head is sold separately.
Q: Are there any other JMC L6 head related products available?
A: We do have plans for such products in the nearest future, but not for now.
Q: Do you also assemble the engine?
A: No. We only sell the head.
Q: Can the aftermarket parts be used with JMC L6 head?
A: All the aftermarket L6 head parts can be used with our product.
Q: Is this production limited?
A: It is not a limited production, but it is expected to be produced in small quantities because the emphasis is put on performance and quality.
Q: In what country/region is JMC L6 head produced?
A: Everything from design to casting, machining, and processing is done in Japan.
Q: EX 3 / 4 seem to have the same size and shape as other cylinders. Why?
A: This is to equalize the exhaust flow speed of all cylinders. As a result, a new water jacket has been installed between the EX3/4 ports, which tend to accumulate heat, to equalize the head temperature between the cylinders.
Q: Does JMC L6 head have the same water jacket as the normal N42?
A: To optimize the cooling efficiency, we have worked on design changes using internal analysis based on full CT scanning of the head.
Q: Do you use the same aluminum alloy as normal N42?
A: After analyzing the normal N42 head, we have adopted the latest aluminum alloy that boasts higher strength.
Q: 11 Is the machining performed on ports?
A: Since it is a new design from casting and the required port diameter is secured at the time of casting, expansion and shaping by machining are not required.
Q: Is the combustion chamber molding machined?
A: Yes, all combustion chambers are fully machined
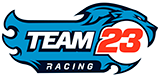
